Iconic jam business blends a rich history with modern techniques
5th December 2024
Wilkin & Sons is world-renowned for its jams, produced in Tiptree, Essex for over 130 years – with its Little Scarlet strawberry jam even finding favour with 007. Sarah Kidby visited the farms and factory to learn more about its enterprise.
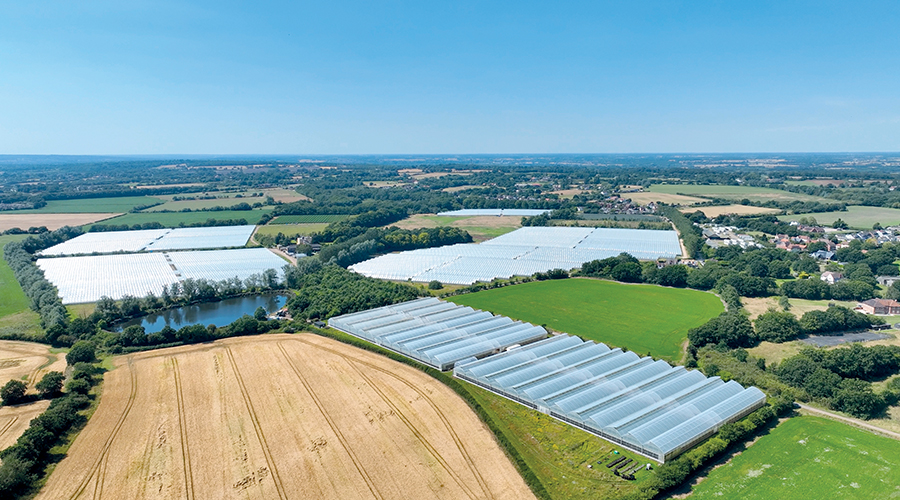
The Wilkin family have been farming at Tiptree for nearly 300 years, moving gradually from arable to fruit growing in the 1860s, and beginning jam production in the 1880s.
According to farm manager Andrey Ivanov, who has worked for the business since 2002, the fruit was once sent to Kelvedon railway station by horse and cart, then on to London, before jam production was brought in-house.
Now, Wilkin & Sons is made up of three farms spanning 263ha, as well as an on-site jam factory, pudding room, storage facility, and packhouse, with an offsite patisserie and pudding company, and an estate of quintessentially English tea rooms throughout East Anglia.

Trees with special importance
The business blends its rich history – which saw the Wilkins grow everything from rare Little Scarlet strawberries, to medlars and quinces, all of which are still grown on the farm today – with modern-day technologies and growing practices, which help to secure its future in an increasingly challenging climate.
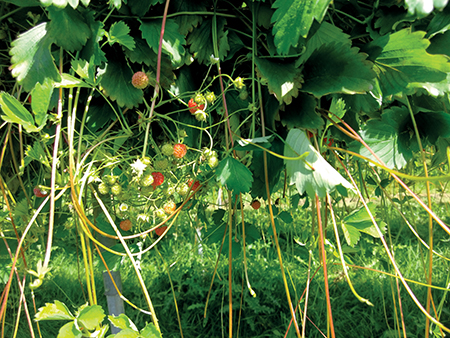
The farm’s 12 established King James mulberry trees are over 100 years old, and another 12 have been planted which will not produce any significant volume for 20–25 years.
Meanwhile, its oldest damsons were planted 84 years ago, the same year that Peter Wilkin, great grandson of founder Arthur Charles Wilkin, was born.
Today, the farm continues to grow a wide variety of fruits alongside strawberries, which are its main crop – including Morello cherries, greengages, crab apples and plums, among others.
The farm’s more unusual fruits and minor crops are made into its jams, conserves, jellies, condiments and other products, which are sold in the UK and exported to around 60 countries.
And whilst the farm has grown many different minor crops over the years, such as blackcurrants and redcurrants, many of these haven’t been replanted, and economies of scale mean strawberries are now its main focus.
A focus on fresh
Despite being known predominantly for its jam, which first received a Royal Warrant in 1911, Tiptree began growing 1ha of strawberries for the fresh market in 2002, which has since expanded to 26ha. Currently the fruit goes into Sainsbury’s – and Tiptree has its own packhouse on site.
“The agriculture and horticulture sectors are very tight at the moment,” Andrey noted. “Margins (where they still exist) are miniscule, so we have to look at economies of scale and we only manage to achieve that with our strawberries.
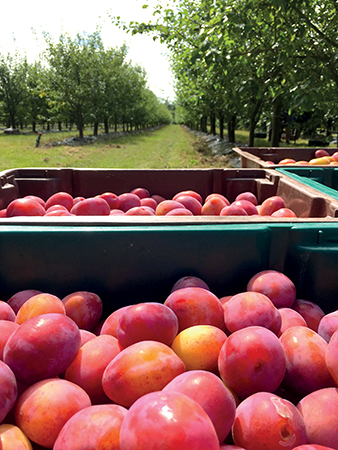
“Some of the smaller growers are disappearing one by one and we don’t want to do that, so we’ve concentrated over the past 10 years on strawberry production and the fresh fruit market mostly. And all the excess fruit goes to jamming – we are very fortunate to have that.”
They now produce around 1,500 tonnes of fresh fruit per year, and 500 tonnes for jam.
Their strawberry varieties this year are Malling centenary, Prize, Aurora Karima and Favori – and every year they trial 3–5 varieties in larger numbers and 5–6 varieties on a smaller scale, usually starting with 50–60 plants.
Within the main varieties, they also utilise three different planting types: bare root, mini tray plants and green plants, to offer a flat profile of fruit seven days a week throughout the season, whilst avoiding large peaks.
Not all varieties are available to Tiptree farms and they have to work with their customers on varietal selection.
Important attributes are: aesthetic, shelf life, sugar levels and flavour, but choosing varieties can be very difficult, as no single variety offers absolutely everything, Andrey said.
Rare variety
Tiptree believes it is the only commercial grower of Little Scarlet strawberries – and its jam gets a mention in the James Bond novel From Russia with Love. The variety was imported by the Wilkins from Virginia, USA, in the early 1900s and has been grown at Tiptree ever since.
Little Scarlets are significantly smaller than traditional fresh strawberries, with an intense flavour akin to that of a wild berry – and it’s a highly valued crop for the farm.
Lacking the size or shelf life for the fresh market, it is grown solely for Tiptree’s Little Scarlet jam. Traditionally a June bearer, it has to be picked, washed and processed within 24 hours.
It was previously grown on the ground, but is now in raised beds to avoid pests and disease (particularly slugs), but unlike the rest of the farm’s strawberries, it is not grown under polytunnels – for now.
The variety is actually less troubled by pests and disease than the farm’s other varieties, but being uncovered, weather is an issue. They tend to have an off year every 3–4 years, Andrey said, and incessant wet weather and reduced pollination this year has hit the crop particularly hard.
Yields are expected to be down at least 50%. As a result, next year they will trial around 2ha of Little Scarlets under polytunnels, but being such a rare variety, it’s not known how changing its microclimate will affect the crop. There’s a concern that other fungal diseases may crop up or that the reduced light transmission could affect plant growth.
The farm’s fruit crops and cover crops in general have suffered this year due to the unseasonable weather – the quinces have had rust on the leaves, though some trees have fared better than others, but the rest of the strawberry varieties were catching up at the time of our visit.
Comparable to desert
Being located in the driest part of the driest county in the UK, water is a key challenge for the farm. In 2022, they had just 511mm of rainfall which Andrey noted is comparable to a desert country.
Last year, it was 912mm, which is still far below the UK average of 1,380mm. And with clay soil, no rivers nearby and very few streams, which generally dry up in summer anyway, there is no underground water to abstract, so rainwater harvesting is their main source of water.
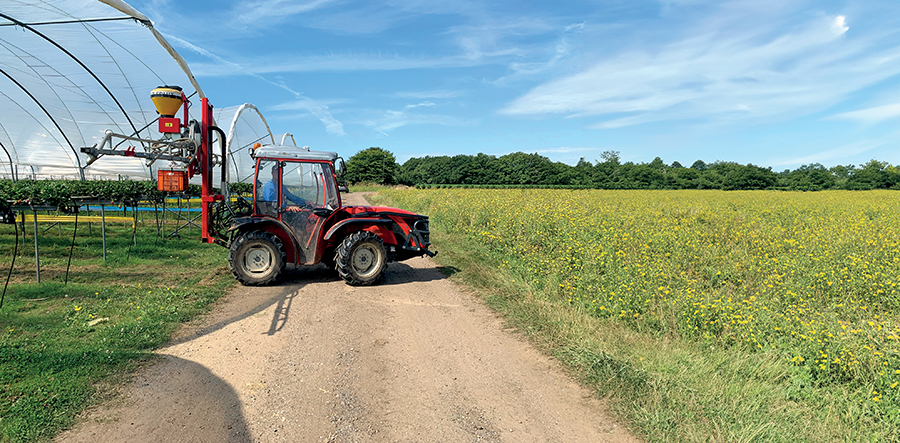
Adopting new technologies has also been important in making the best use of their water. Up until 2002, their production methods were very traditional, with fruit grown in open fields, but now all strawberries apart from the Little Scarlets are grown in tabletop systems under polytunnels, in coir substrate. Sensor technology is used to provide irrigation only when the plant needs it.
The farm has seven reservoirs across its farms, and water is harvested from all of its structures, including greenhouses, polytunnels and its ‘New Growing System’. A treatment plant also allows them to reuse waste water from the factory for irrigation, and prevents any bacteria or fungal diseases from the field being spread to the whole farm. The central pumping station is at the heart of the Tiptree estate – connecting the farm’s reservoirs and irrigating its crops.
“We needed to do a lot of work on water, and now I can say we are water resilient,” Andrey said. Thanks to their harvesting of water and precise irrigation, as long as they have 650mm rain a year, they are self-sufficient.
“We’ve done this because we had no other choice, but we’re very proud of it because now the next challenge for everyone will be water – a lot of farmers are struggling,” Andrey added.
Cutting back on sprays
The farm has two independent agronomists who visit the farm on alternate weeks.
As a conventional grower, sprays are used according to the weather and need of the crop, but they have been using biological controls for the past five years, which are working very well, and pest monitoring traps are also used.
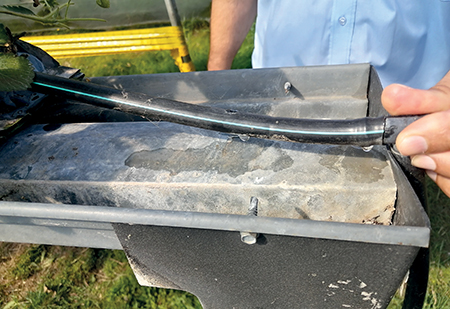
Insecticides have been reduced by 95–100% as a result, but Andrey stressed that it’s dependent on pest pressure and if they could not establish biological control, they would have to spray.
Fungicides, on the other hand, are more difficult to reduce and each year is different – botrytis spores are in the environment so if the conditions are right, with wet weather and humidity over 60–70%, it will start to cause problems.
The same is true for powdery mildew, which is their biggest disease pressure for the strawberries. They are trialling UV-C treatments over the next two years and this has already reduced their fungicide use by 50%.
While consumers are often concerned about spraying, Andrey said UK regulations are strict and the demand for British food from countries such as China shows that the Union Jack carries a promise of safety and quality.
New Growing System
In 2015, Tiptree became the first grower in the UK to introduce its ‘New Growing System’ (NGS) – a covered oscillating structure first seen in Spain that allows them to mechanically move layers of strawberries up and down at the touch of a button, with fully integrated climate control.
Vents on the top and sides automatically open when temperatures rise.
Often referred to as the ‘Tiptree vertical system’ by visitors to the farm, it’s not actually vertical – during the growing stage the layers of strawberries are grown together, and they can be moved up and down to allow pickers to interact with the fruit, creating a better environment for workers.
The development wasn’t cheap, but the rewards for the business have made it a no brainer. It allows them to crop 100% of the production area and increase plant density, unlike in a conventional system where you can only crop every second row.
Traditional growing in open fields allowed them to plant 30,000 strawberry plants per hectare, while tabletops extended this to 55,000/ha. But with the new system, they can plant 200,000/ha – though Andrey says the optimum number is 100,000.
Insufficient light levels in the UK meant the plants were too vegetative and fruit yields too low with both 200,000 and 150,000 plant/ha. Yields have increased 50% with the NGS, and their carbon footprint has reduced threefold, compared to tabletop systems.
They can also start the season earlier and finish later without artificial heating and lighting, and a much more tightly controlled climate means zero insecticides and herbicides. While fungicides are still used, it’s hoped the UV-C treatments will eliminate this too, so they can claim to be residue free.
Following a carbon study, they are now planning a similar 4ha structure closer to the factory which will collect heat from the chimneys and boilers to use for growing – this will extend the season for another 6–8 weeks. Light levels will prevent them growing too early, but beginning in April and continuing until November is sufficient, Andrey said.
Being a business with a farm, rather than purely a farm, gives Tiptree an advantage when it comes to new developments such as these, he acknowledged – they have access to engineers, accountancy, HR etc, whereas for many growers, all these tasks fall to the farm owner.
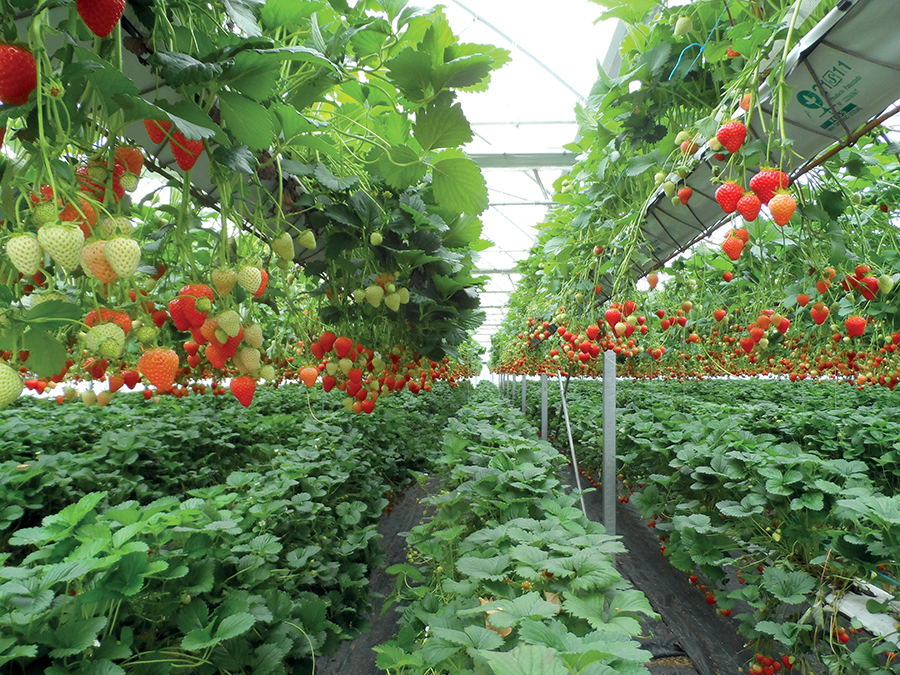
Carbon calculations
The business has taken pains to save energy and improve its carbon footprint – carbon calculations are now in their fourth year, which has been a huge undertaking, Andrey said.
They have also carried out field scans to identify retained and active carbon to better understand their soils, and will plan methods of putting carbon back into the soil over the next two years.
Following these calculations they decided to ‘inset’ – rather than offset – their carbon footprint, i.e. making changes to their own site rather than buying woodland for example, though this will be much more time consuming and costly.
As a farming enterprise, Tiptree is now in carbon credit, but as a company, Wilkin & Sons is a long way from this goal due to the energy intensive nature of jam production, particularly the glass jars.
A former arable field has been put into solar panels and another, opposite the strawberry polytunnels, is in regenerative agriculture.
Tiptree is in Countryside Stewardship Mid Tier and farms to LEAF (Linking the Environment and Farming) standards, adding biodiversity corners and edges wherever they can, including owl boxes on site and leaving hedges and grass uncut as much as possible to increase biodiversity.
Subsequently, the farm has become a haven for hares, pheasants, partridges and muntjacs, among other wild species. This has the added benefit of attracting natural beneficials to combat pests. Providing habitats for pests has also been successful in keeping them away from the fruit crop, Andrey explained.
The crop type planted in each field is changed every two years to maintain vigour and yields, but noting the current buzz around regen ag, Andrey said farmers have been using these techniques for generations.
“It’s inevitable that you cannot put the same crop on the same field year on year, so to have that success you have to recharge the soil with different crops – whatever you choose, wild-flowers etc, depends on what you need for your soil. We have been doing this for generations and generations, it’s not something new really but that’s the new modern word that gets everyone excited.”
He added: “Now we’ve got much more modern methods of assessing the soils to decide what to do to get everything back up to scratch.”
The farm does regular soil health tests and field scanning to understand the nutrient content and health of the soil, sending leaf, soil and water samples every 2–3 weeks and adjusting as needed. Each field has sensors that constantly measure inputs such as moisture, pH, and electrical conductivity, which is connected to a system in the pumphouse, automatically giving the plants exactly what they need.
Recruiting workers
Tiptree has 13 permanent members of staff and all other labour for the farms is sourced through the Seasonal Agricultural Worker Scheme (SAWS) – in fact, Wilkin & Sons was the second registered user of the original scheme when it first opened in the 1950s.
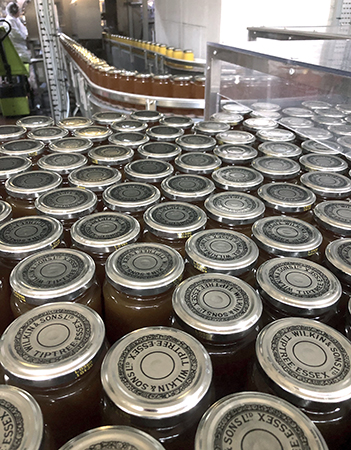
It closed in 2014 but reopened as SAWS after Brexit. Whilst the farm has no problem finding sufficient labour in terms of numbers, getting skilled, experienced pickers is an issue, as many of the workers are new to the scheme.
Seasonal workers live in the on-site farm camp, which includes furnished caravans and a recreation and catering facility, plus a laundry, drying room and meeting hall.
The farm has around 20–30 workers on site from February each year when the polytunnels are put up, but once harvest gets started, numbers can run into the hundreds at peak times.
Harvest begins each year with the Timperley Early rhubarb in April, followed by cherries in June, mulberries in July, greengages in August, damsons in September, quinces in October, medlars – a Mediterranean fruit with a savoury flavour – in November and apples from August to September. Meanwhile, strawberries are harvested from May to October.
There are more than 150 workers in the factory year-round, many of whom are friends and family of the permanent staff, who help out during the holidays – and they also have workers on zero-hour contracts, explained factory supervisor Tracy Warren, who manages the pudding room and marmalade making.
Jam production
When it comes to jam production, everything is made to order. While they used to cook from fresh, with orders getting larger they now individually quick freeze (IQF) fruit after picking. Again, they have their own storage facility, which was built in 2012.
Being as self-sufficient as possible in farm-grown fruits is important to Tiptree.
They are often asked if the fruit used for the Tiptree products is grown on the Tiptree farms, and whilst they try to ensure that this is the case for the fruits they can grow on the farm, some is bought in to meet demand or, for fruits such as the Seville oranges used for marmalade and vine fruits for Christmas puddings.
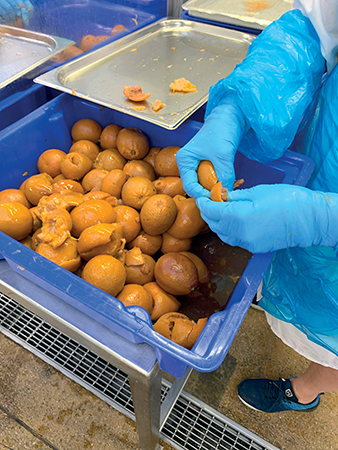
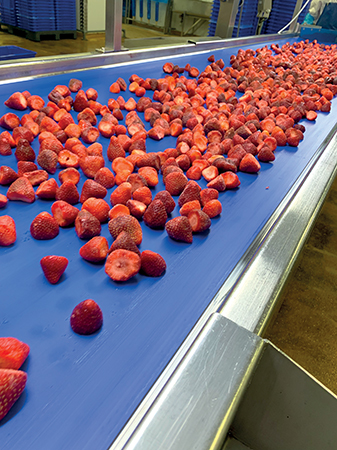
The fruit begins its journey in the factory by being put through a conveyor belt, allowing staff to check it and remove any stones in plums or cherries. before it’s weighed, washed and processed. The factory also has a destoner machine for the Morello cherries.
For the marmalade, oranges are cooked for three hours and left overnight to release the liquor; they are then pulled apart by hand to check for pips and the pulp and juice are removed, before being added back into the final product with the cut peel. Every part of the orange is used apart from the pips, Tracy said.
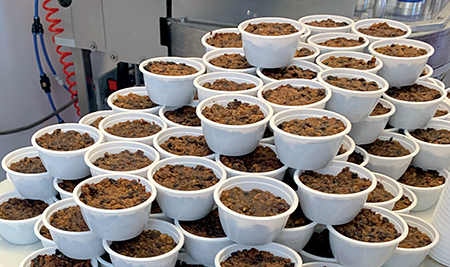
Also produced on-site is the company’s wide array of other products – from curds and sweet spreads, to fruit jellies, chutneys, relishes and sauces, among many others. Additionally, Tiptree produces English spirits and liqueurs.
The on-site pudding room, meanwhile, is where its range of Christmas puddings are created, including Tiptree’s own brand varieties and Cole’s nut-free puddings, which became part of Wilkin & Sons in 2010.
The fruits are pre-weighed 24 hours before use, soaked in the alcohol and hand weighed again before being put into basins and into the cooker, which has internal probes to check the temperature.
After overnight cooling they are packed, again by hand and checked on a sample table to ensure quality.
On the horizon
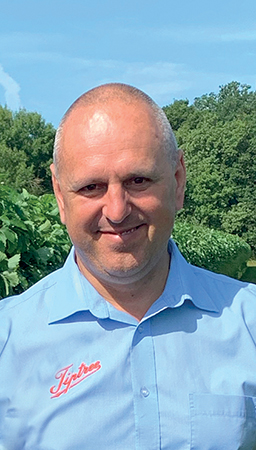
Tiptree is always looking ahead, and next on the horizon the business is looking to add nut butters to its extensive product list. By the end of this year, there will also be an announcement on its Royal Warrant, with hopes this will be renewed by King Charles.
Finally, on the farm side, Tiptree is looking to trial robots to aid early disease detection in its crops.
Grower profile
Farm manager: Andrey Ivanov
Location: Tiptree, Essex
Fruit growing area: 263ha across all three farms
Fruits grown: 30ha strawberries, and 25ha in rhubarb, raspberries, cherries, apples, greengages, Victoria plums, damsons, mulberries, quinces and medlars
Soil type: Silty clay
Visit the Tiptree website for more information.
Read more grower profiles
Read more fruit news