Driving change: Advanced mechanical harvester showcased to vineyards as UK wine industry evolves
9th March 2025
Fruit & Vine recently spent a morning at Greyfriars Vineyard in Guildford, Surrey where NP Seymour hosted a demo day for customers to see the latest ERO harvester in action, and invited ERO along to talk through the technical aspects.
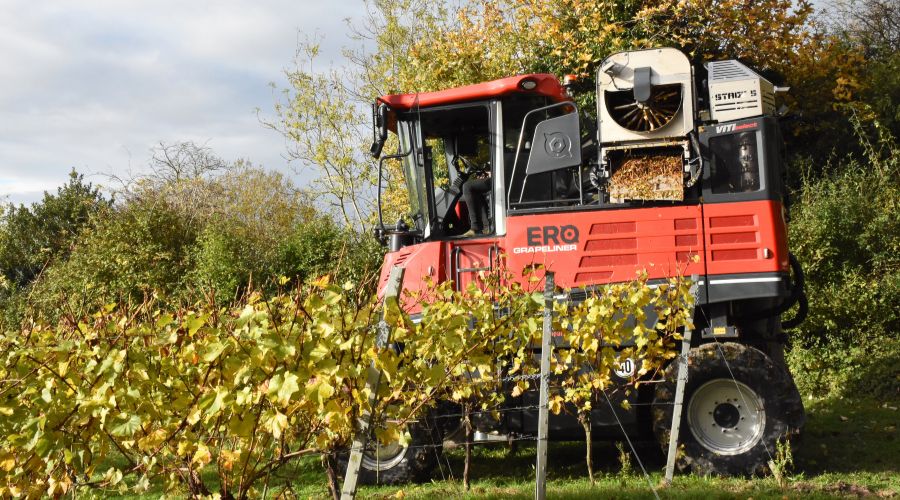
With an expanding contracting business, Sam Barnes, founder of SJ Barnes Ltd, is already well-versed in the benefits of mechanical harvesting over hand picking in terms of both time and labour cost, having previously operated a trailed Pellenc 890 bought in 2019 with a second of the same model being purchased two years later. So, for Sam, making the move to a self-propelled machine, complete with all the latest aids and technology, is really just a matter of making sure that the maths work.
Sam has a long working history with viticulture machinery specialist, NP Seymour Ltd, so his first port of call was their knowledgeable sales staff, which resulted in a trial of the ERO Grapeliner 7200V.
Technical specs
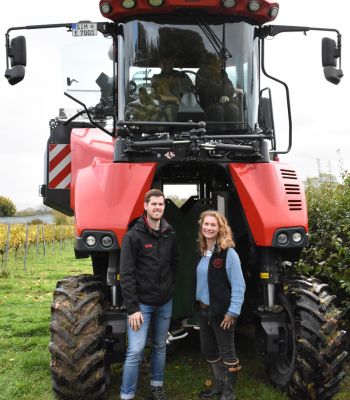
On the day of Fruit & Vine‘s visit, ERO sales rep Lukas Zimmermann was in attendance, to explain the technical aspects and share the experiences of vineyards using the machine in other countries.
“The machine is very efficient; it can pick a hectare in 1.5–2 hours, and has a three-stage cleaning system consisting of a leaf ejection system that blows 70% of the leaves out using a cross air nozzle and a leaf rake.”
A bottom suction fan catches some of the leaves that make it through before the fruit is conveyed upwards, and there is a suction fan positioned on the cross conveyor belt to remove any remaining leaves or debris. This system is optimised to ensure that juice loss is minimised.”
Also available is an optional de-stemmer and grape sorting system, which can be monitored and adjusted from the touchscreen in the cab. The de-stemmer can easily be turned off, if not needed, at which point the grapes are redirected straight into the tank.
The 7000 series has been in production since 2018, and the model trialled by Sam is 200hp, hence the 7200 designation. There is also a 175hp version, which Lukas explained would be suitable for easier, flatter terrain.
“If conditions are good, the 7200 can handle inclines of up to 40% and lateral differences of around 20%, but there is a display in the cab to tell you if you are approaching the limits,” pointed out Lukas. “The fruit tank on this particular machine is 3,000 litres, but there are other options available with 2,200 and 2,600 litre tanks, which also makes the machine smaller and therefore more suitable for vineyards with narrower widths.”
The tank is situated centrally for better weight distribution and centre of gravity, and unloads from the side making it a quick and easy process for the operator, and a gentle process for the fruit.
The self-steering system works with a combination of ultrasonic and mechanical sensors that detect the location of the vines and feed this back to the machine, which then steers accordingly.
Power is provided by a six-cylinder, six-litre, electronically-controlled Deutz engine located and designed in such a way that all service items can be accessed from one side of the machine.
For ease of cleaning and maintenance, all covers have been designed to be removable without the need for tools. On the road, the 7000 series can be driven at up to 40kph (optional), with the standard model offering 20–25kph road speeds, and the suspended front axle ensures that this remains comfortable for the operator.
The cab is sound insulated, and vibration damped. It offers good space with great visibility and is air-conditioned with a refrigerated compartment as standard.
The manual levelling system allows for up to 750mm of travel and the fuel tank is 340 litres, with the machine being designed to use lower engine power while harvesting for improved fuel consumption and longer working periods per tank. The total machine weight is 9,500kg with the de-stemmer, or 8,970kg without. ERO also offers a 5000 series of machines, which are slightly lower spec and therefore offer a more cost-effective solution, Lukas concluded.
Operator opinion
We jumped onboard the ERO 7200V as Sam was working the vineyard to find out a little more about his business and, more importantly, how
he was getting on with the harvester trial.
“I have been offering vineyard contracting services since 2017, with my family working in the industry for three generations,” explained Sam. The business is based in Biddenden, Kent, and the team tends to harvest mainly around the Kent, Sussex and Surrey area, although Sam points out that they are happy to travel further afield if required. Sam offers a full range of services from vineyard establishment (Sam had the first GPS-guided planting machine in the UK back in 2020), right through to harvest.
“We have found mechanical harvesting to be very successful over the last five or six years that we have been operating our trailed machines.
“The ERO was used on trial during the latest harvest, although 2024 hasn’t been the best harvest, with yields lower than usual. So far, I have been very impressed with the performance of the harvester. It’s very easy to use once you know how to set it up, and the self-steering does a very good job of keeping the harvester on track.
“It doesn’t self-level, but to be honest I think that is better, as it moves with the contours of the vineyard and therefore the vines, rather than staying upright. Height is also set by the operator and there is a useful setting function that allows you to set numerous parameters, depending upon the vineyard, vines or grape variety, and it will return to these settings with just the push of a button.”
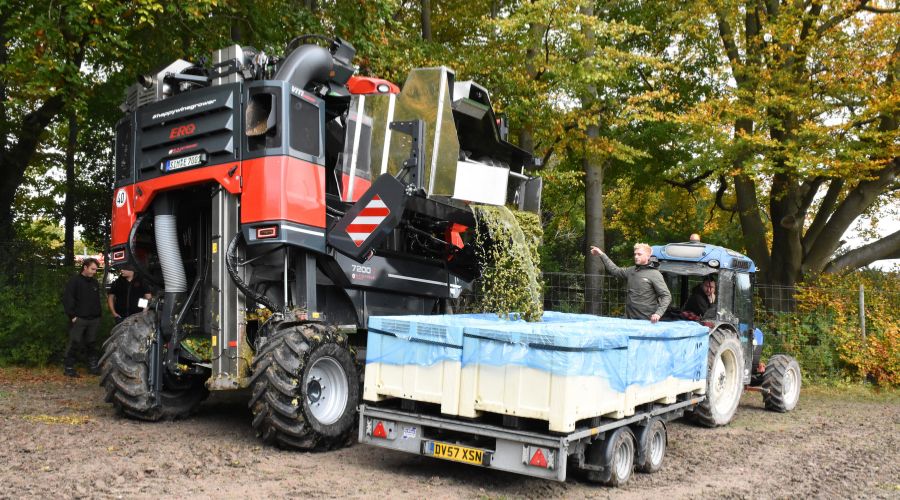
Sam explained that he tends to run it at around 4.5kph, but points out that it will still work effectively at faster and slower speeds, between 3.5 and 5.5kph, with the optimum speed ultimately down to the individual job, the conditions and the grape variety being harvested. Sam reckons that the fruit shaker mechanism works well. The machine is delivered with 7 x 2 = 14 shaker rods, but it can also be operated with for example 2 x 4 = 8 (according to the size of the fruit zone).
He comments: “It is very manoeuvrable, with the front wheels almost turning 90-degrees, so that it can turn around in almost its own length, which is very useful in compact headlands. It does a decent job of dealing with any rotten fruit.
“If rotten fruit is dry it tends to leave it on the vine, although if it’s wet it will take some through to be dealt with at the winery.”
The harvester is equipped with cameras that show the operator where the vines are, with infrared sensors to keep the machine on track and Sam explained that he really likes the driving position which puts you right over the vines being worked, and the glass floor that allows you to see exactly what’s going on below.
Our brief run in the machine confirmed that the cab is a comfortable environment to work in and the noise levels were very good. The glass floor is, indeed, a great feature, but care is needed to avoid it becoming caked in mud, as it was on our demo day.
However, this was undoubtedly due to the high footfall on the day, and a single owner/operator should have no trouble keeping it clear.
Dealer view
NP Seymour is the first dealer in the UK to offer the 7000 series and we caught up with Claire Seymour to get her take on the harvester.
“Where the ERO really stands out over other harvesters on the market is in the cab, and especially the central position that it puts the operator in, and the excellent visibility that this provides,” explains Claire.
“The industry is moving on rapidly and we are adapting to that by offering larger harvesters and machines that can work quickly and efficiently, especially given the weather windows that we must work with here in the UK. It is also very clever in the way that you can change settings depending upon what variety of grape you are working with.
“When it comes to options there are a few to pick and choose from; but there are some that you would definitely not want to leave off, such as the auto steer and the cameras,” Claire advises.
Growers and wine makers are certainly coming around to the idea of machine harvesting. Even just five years ago there was a certain amount of reluctance to embrace this kind of technology here in the UK, but now there is the realisation that to remain sustainable you need to mechanise. There is also a change in drinking habits and growing conditions, so no longer is the UK all about sparkling wines as there is good quality still wine being produced too, Claire points out.
“The wineries are also now generally better equipped to deal with the large quantities of fruit delivered at a time with mechanical harvesting. NP Seymour is committed to providing the best possible technology for the modern-day grower. We have a long-standing relationship with ERO, and have been supplying their vine trimmer and de-leafers since around 2008. We have been impressed with the quality, reliability and technology that ERO machines deliver, and the way that they are always looking to improve by researching, running trials and working with growers. They also offer great support and backup when its needed.
“In short, we think there is nothing else on the market that can beat them. While the machine is a significant investment, payback can come quickly when considering the time and labour savings that it brings.”
Read more vine news.