Growing blackcurrants amid increasing climate challenges
26th October 2023
With the UK’s climate shifting towards more extreme weather, growing blackcurrants is becoming increasingly challenging for sixth-generation farmer Nick Overy, whose family has been producing the crop under contract with Ribena for 30 years.
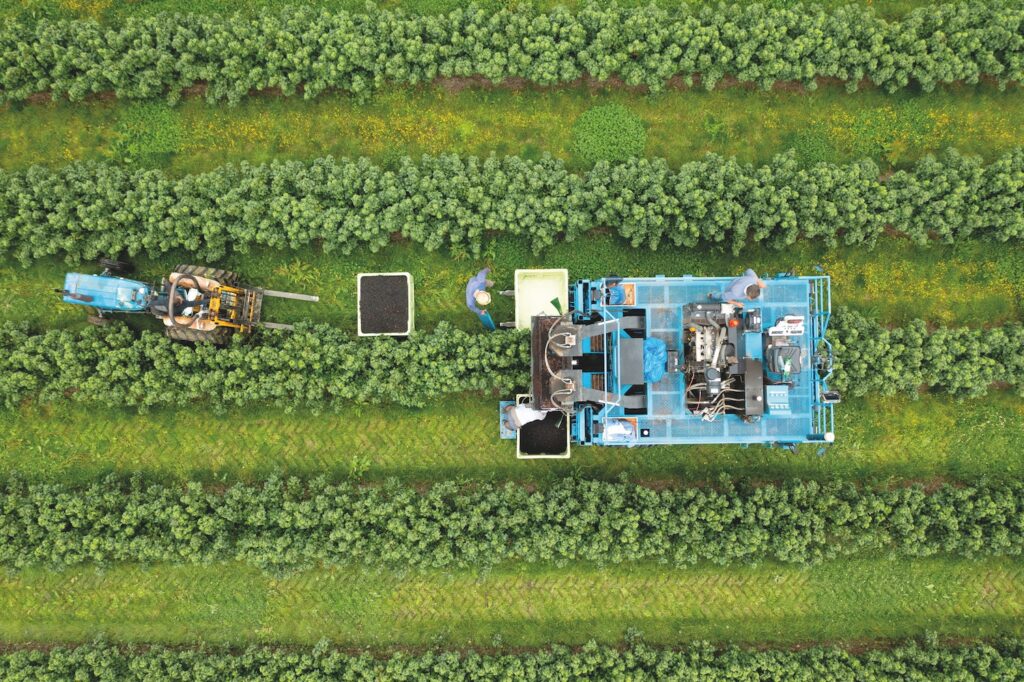
Nick and Ian Overy of Nursery Farm in Matfield, Kent as they begin the harvesting of Ribena’s blackcurrants at their farm for 2021.
- Farm : Mascalls Court and its three satellite farms are run by Nick Overy and his father Ian
- Location : The main farm is based in Paddock Wood near Tonbridge, Kent; with additional land in Brenchley, Matfield and Horsmonden
- Total size in ha : Around 180ha across the four sites
- Type of fruit grown : Blackcurrants are grown on approx. 45ha, with 7ha of Gala apples; the rest is divided between arable crops including wheat, oilseed rape and beans, as well as grassland used to make haylage for horses
- Varieties grown : The farm grows seven different varieties of blackcurrant, all developed by Ribena at the James Hutton Institute. These are: Ben Gairn, Ben Starav, Ben Klibrek, Ben Avon, Ben Hope, Ben Alder and Ben Tirran
- Soil type : Light, sandy soils (satellite farms) as well as clay (Mascalls Court)
Previously home to hops and livestock, Mascalls Court Farm in Paddock Wood, Kent, now boasts arable crops, rows of Gala apples and blackcurrants, with the majority of fruit grown on satellite farms in Horsmonden, Matfield and Brenchley.
According to owner Nick Overy, whose family have farmed at Mascalls Court since 1848, the first blackcurrants were planted in the early 1990s, shortly after the farm stopped growing hops. Explaining the reason behind the choice, he said the crop fitted in well with other operations on the farm.
Lighter soils preferred
While some blackcurrants are grown at the main site, most of the fruit comes from holdings on the Tunbridge Wells sandstone ridge, as blackcurrants tend to prefer lighter ground as opposed to heavier clay soil, Nick explains.
Soil health is monitored through nutrient testing every four years, and leaf samples are taken for trace element deficiencies. To optimise performance, magnesium, phosphate and potash levels are topped up regularly, and nitrogen is applied at pre-flowering, post-flowering and post-harvest (Nitro Chalk 27.5% N) at a rate of 520kg per hectare total of product.
Of the total blackcurrant hectarage at the farm (45ha), between two and five hectares are replanted each year on fresh ground to maintain production at optimum levels, Nick adds. This is typically done around January/February time by seasonal workers while the bushes are dormant.
“Blackcurrants take a lot out of the soil, so we tend to put the land into arable for four or five years before we replant it, or we use ex-apple ground,” he says.
“If we grub up an orchard, we can put it straight back into apples; but you can’t pull out a blackcurrant plantation and replant it immediately.”
Blackcurrants usually stay in the ground for 15–20 years, and rely on pollination by insects to produce the fruit. To attract more beneficials to the crop, Nick has established wildflower meadows around the farm and keeps headlands uncut for at least two years.
To enhance biodiversity and encourage more wildlife onto the farm, the team has also built over 60 bird boxes and six barn owl boxes across the four farms. In addition, the farm has been enriched with more than 300 metres of new hedgerows and countless trees over the last two years, and an area of woodland is coppiced annually to encourage young growth.
These are some of the key actions suggested by Suntory Beverage and Food GB&I (SBF GB&I – Ribena’s owner) as part of what is called the ’Six Point Plan’ put in place to help growers produce blackcurrants more sustainably.
Targeted spray programme
Nick uses a robust spray programme to keep pests and diseases at bay, starting with a round of Scala, Signum and Switch through flowering in April and May to control leaf spot and botrytis.
After flowering, we tend to stop spraying as it is difficult to travel without doing damage, as the bushes lower their branches with the weight of the fruit,” he explains.
Planting disease-resistant varieties developed through the James Hutton Institute’s (JHI’s) breeding programme has also helped reduce disease pressure and deter major pests such as the big bud mite.
The crops also respond well to foliar feeds like Maxicrop, which is applied through flowering and after fruit is formed, Nick adds.
Frost is generally not an issue with blackcurrants, as they tend to flower later in the year when the risk is much lower.
“Our main problem with the climate is getting our chilling hours. We have to have 2,000 hours below 7oC while the bushes are dormant to help with even ripening, and as we’re getting warmer winters, it’s becoming more of a problem.”
Climate shifts
Blackcurrants thrive in cooler climates, and as the UK has been experiencing hotter and dryer summers, growing and harvesting the crop has become increasingly challenging for producers.
“Last year, we experienced over 40oC during the harvest, so that led to some fruit drop,” Nick says. “And then we had a very dry summer, which didn’t help the fruit bud for the following year, because we don’t irrigate at all.
“So we’re struggling with hot, dry summers. You certainly need a lot of water after harvest,
and we haven’t been getting that.”
While more sunshine hours increase the sugars in the fruit, excessive heat has meant that staff had to race around to finish the harvest before the fruit fell on the ground, which was unprecedented in the farm’s blackcurrant-growing history. However, Nick is expecting the issue to become more frequent in the future as climate change unfolds in the UK.
The wet weather this spring has also affected flowering and pollination of blackcurrant crops, and increased the risk of botrytis rearing its head, he notes.
A year on the farm
Blackcurrants require care and maintenance all year round, and work begins with the planting of new bushes between January and February. Spraying will then follow in early spring as soon as leaves start emerging to protect the crop from leaf spot and botrytis. Plants will also be given seaweed-based foliar feed around this time.
The timing of nitrogen applications is becoming more crucial with the drier weather and is determined by rainfall, Nick explains. The first dose is typically applied prior to flowering, followed by a second dose around a month later and a final application post-harvest.
Nick explained having a range of different varieties is important to stagger the harvest, so not all fruit is picked at the same time.
“All the research and development for the varieties is funded by SBF GB&I at the James Hutton Institute in Scotland, and all the varieties are owned by Ribena,” he added.
90% of the blackcurrants grown in the UK go into making Ribena, which means around 10,000 tonnes of blackcurrants are produced annually for the popular fruit and drink concentrate.
The company has invested heavily in research work at the JHI to develop new climate-resistant blackcurrant varieties that offer a more robust disease and pest package to combat emerging challenges.
Among the new varieties is Ben Lawers, which has been found to crop well despite warmer winters, helping growers overcome a major sustainability challenge.
On the farm, Nick produces around 300t of fruit for Ribena each year, picking 20–25t per day during harvest season. The fruit is typically processed within 12 hours at the Thatchers cider factory in Somerset, after which it heads to SBF GB&I’s factory in Coleford to be made into fruit juice.
As soon as harvest is finished, the bushes are trimmed and sided up with a bush trimmer to increase airflow between the rows and reduce disease pressure. Plants that have reached seven to eight years of age are cut all the way down to the base to rejuvenate the bushes.
The final task of the year is weed control, with spraying carried out in December and the following March.
Machinery fleet
Due to the large quantity of fruit produced, blackcurrants are picked by a machine harvester, which was purchased new in 2009 from Somerset Fruit Machinery. It’s a highly-efficient way to harvest the fruit and well-suited to large commercial farms, requiring only two operators.
“As well as a driver, we only need two guys on the back of the machine to sort the odd leaf that comes through, that’s all they do on the back and change the bins over,” Nick explained.
The harvester is accompanied by a two-row blackcurrant sprayer, which was custom-built by Andreoli Engineering in Italy with the input of
Nick and the team, based on the company’s existing Tristar sprayer.
The only other piece of machinery specific to blackcurrants on the farm is the side-trimmer, which comes from Holland and is designed to shape the bush by cutting off the lower branches.
Like other growers, Nick has had difficulties sourcing equipment since Brexit, and a lot of the machinery is shared between the orchards and blackcurrant fields. These include the tractors, weed spraying equipment and fertiliser spreader, which uses GPS technology to optimise fertiliser application by automatically calculating the desired flow rate.
The GPS spreader is the farm’s latest purchase and will be trialled for the first time this year,
Nick shares.
“Previously, we were just blanket spreading the fertiliser on as needed, but we’re looking at going down the GPS route for certainly putting our phosphate, potash and magnesium on.”
Minimal staff
At present, Nick and his father Ian are the only full-time workers looking after blackcurrants on the farm, with Nick’s son Henry set to join the team after finishing his degree in agriculture at Newcastle University and following some travelling.
A truly family-run business, Mascalls Court Farm only employs a small number of casual workers to carry out seasonal tasks, who return to the farm every year.
“We have three guys come for the blackcurrant harvest, and when we’re not picking blackcurrants, we’re harvesting apples, at which time we’re joined by four more who come for apple picking in the beginning of September – so then we have a total of seven,” Nick says.
“And then during the winter, we have three guys come for blackcurrant planting in February.”
Headlands and hedges are cut every other year, and some contracted work is hired to help with the pruning of apples as well, he added. On the agronomy side, the farm works with specialists from Hutchinsons who walk the orchards every two weeks during the growing season. For blackcurrants, Nick consults Rob Saunders, also from Hutchinsons and who worked at SBF GB&I as an agronomist, as and when needed, who offers advice through weekly phone calls throughout the season.
Thoughts for the future
When it comes to blackcurrant growing, Rob believes the challenges that stand before the industry are three-fold. Climate change is undoubtedly the biggest of those challenges, with further increases in warm and wet weather predicted for the coming years, necessitating
the development of more varieties that can cope under these conditions.
The loss of the plant protection armoury available to growers is also high on the list, Nick said, and could mean it will be more difficult to control yield-robbing pests and diseases in the future. Labour is also a concern, more so for orchards than blackcurrants, and there is an urgent need for change in government policy to replenish the UK’s depleted seasonal workforce.
“I’ve got some of my apple pickers who have been with me for 14 years, and they only come for around four or five weeks and then go home again,” he noted.
“Unless the government changes, I think we’ve got two more years and then that’s going to finish.”
Regarding future plans, Nick is hoping to maintain the farm’s current blackcurrant production and remain a part of the Ribena family. “Blackcurrants are vitally important to our business, and we hope that Ribena will continue sourcing their blackcurrants from the UK.”