Hall Hunter brings automation to blueberry production
21st August 2024
Hall Hunter, one of the leading berry producers in the UK, has a progressive and visionary outlook to fruit production. Machinery editor Neale Byart visited to see the grower’s latest machinery in action.
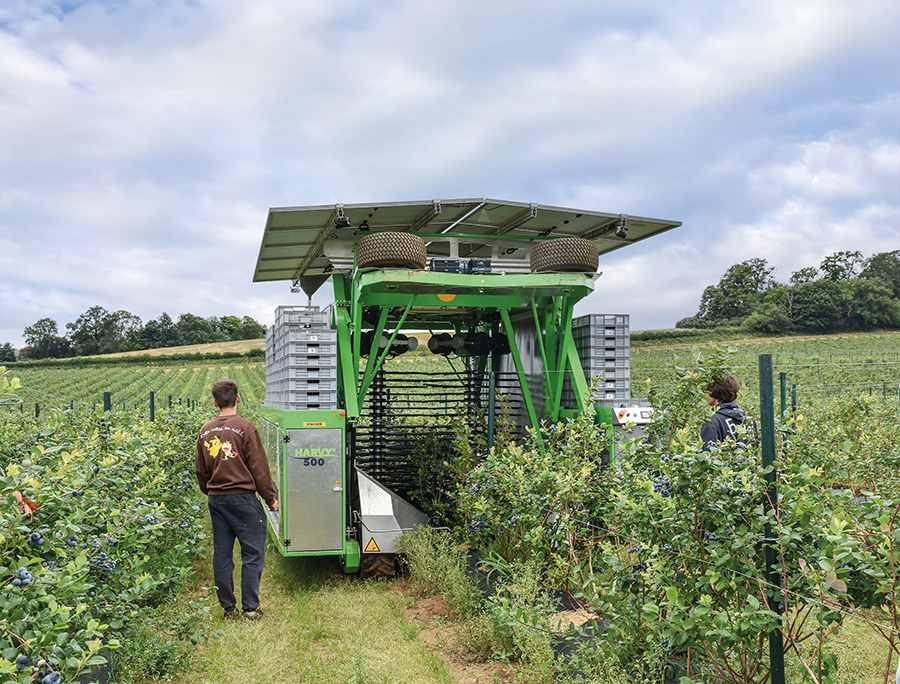
Founded back in 1966 by Mary and Mark Hall on Hearthlands Farm in Wokingham, the company now grows a variety of fruit across four sites in Berkshire and Surrey.
The largest of these farms is Tuesley Farm in Surrey – home to Mary and Mark’s son Harry, who now runs Hall Hunter. On this site Hall Hunter grows strawberries, raspberries, blackberries and blueberries, with the latter taking up the most hectarage.
The UK market consumes around 60,000 tonnes of blueberries per year, with around 6,000 tonnes of those grown in the UK. Of these, Hall Hunter will produce around 2,400 tonnes of blueberries in 2024, growing to 4,000 tonnes as the crop matures over the next few years – making them the largest individual grower of blueberries in the country.
The UK market for blueberries is currently growing at around 25% year-on-year as consumers wake up to the fact that not only are they delicious, but they are also considered to be one of the ‘superfoods’ due to their high levels of vitamins, minerals, fibre and antioxidants. The rest of those sold in the UK currently come from Peru, South Africa, Morocco, Portugal, Spain and Eastern Europe.
Until recently, all blueberries at Tuesley farm have been picked by hand, and this tradition is set to continue in the main, for the foreseeable future; but there is a change coming, in the form of the Harvy 500 mechanical blueberry picker from Fine Field Innovative Agri Solutions.
However, picking is not the only part of the process that Hall Hunter has looked to streamline through automation. They have also added an automatic grading and packing machine in their packing house and, on the day of Fruit & Vine’s visit, were trialling some autonomous robots to take the berries from the field to the packing house.
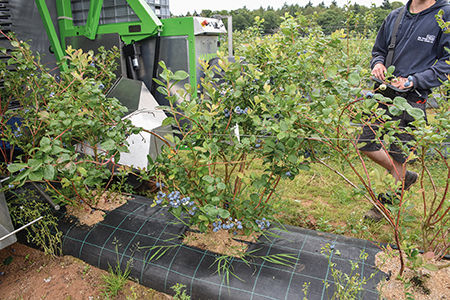
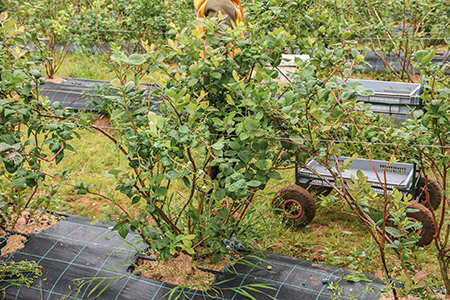
Jim Floor, managing director of Hall Hunter explained: “The Harvy 500 is the only one in the UK. We took delivery last season, but this is really the first year we have used it in anger.
“There are other similar machines on the market, as anyone who has watched Clarkson’s Farm will know, but we believe that the Harvy 500 is the best machine available and the guys that designed it are operators of a blueberry farm themselves so, although similar, this one has been specifically produced with blueberry harvesting in mind.”
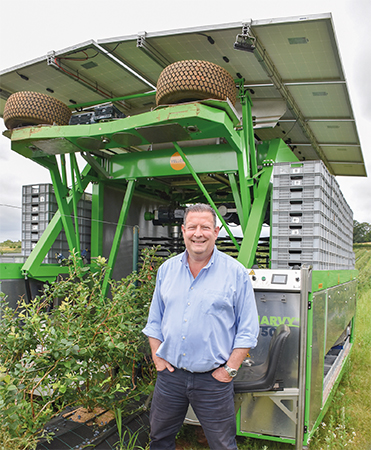
Jim points out that developing a machine to pick blueberries is very difficult, specifically when it comes to matching the dexterity used when picking by hand. Although the machine can work much faster than its human counterparts, the downside is that it will take everything, so you get some unripe berries picked that a hand picker would have left on the plant.
“This is where our new grading machine comes in, as it takes a harvested crate of blueberries, including any unripe berries and the odd leaf, and picks out just those fruits that are in good condition and ready for the market,” Jim said.
“The machine uses a colour monitor to remove the unripe fruit, and a camera that can detect damaged berries with a high degree of accuracy.
“The unripe or damaged berries are rejected, while the approved fruit then goes on to be weighed and packed into a punnet. We probably lose around 10% of the total fruit yield due to being picked when unripe, along with other losses, but with a picking rate of around 500kg an hour, compared to a typical 10kg per hour for the average hand picker, the Harvy 500 is doing the work of around 50 people; so, despite the initial high outlay, the sums do add up.”
Developed for machine harvesting
On the day of Fruit & Vine’s visit, the machine was in action just up the road at Binton Farm – a new venue for Hall Hunter which is rented and used mainly for blueberries, but which also houses their raspberry nursery.
It has very sandy soil and has been in development since last autumn. Here, there are a mixture of some new beds, which are ready for planting in the autumn, and other fields with plants ranging from one to four years old, transplanted from Tuesley Farm.
Machinery editor Neale Byart visited the UK’s largest blueberry producer Hall Hunter Partnership to see the company’s new blueberry harvesting machine, as well as automated grading/packing machine in action 🫐 #fruit #fruitfarming #fruitPicking #Blueberries #HallHunter pic.twitter.com/W8FH68XKmt
— Fruit&Vine Magazine (@FruitandVineMag) July 25, 2024
One field has been planted with a variety of blueberry that has been specifically developed and grown for machine harvesting, although they won’t be producing fruit in harvestable numbers for two or three years. These plants, a variety called FC 1164, grow in such a way that makes them particularly suitable for machine harvesting.
Most importantly, all the berries mature at the same time, so that it only needs harvesting once when all the berries should be ripe, reducing wastage. They also retain the berries on the plant better, to reduce shedding losses, and they have a growth habit which is more upright, allowing the machine to operate tightly against the stem.
There is a significant investment in plants, but each should have a lifespan of around 15 years.
To demonstrate the Harvy 500, Hall Hunter were harvesting on standard blueberry plants, which would normally be hand-picked. Despite this, the machine did a very impressive job. The ‘brushes’ rotate and move up and down as the machine moves along the row, replicating the actions of a hand picker.
The machine is loaded with empty crates on both sides, which are automatically rotated as they fill, starting with stacks of empty crates on each side of the machine and finishing with full crates in the same position.
When full, it provides a maximum capacity of 1,000kg. The machine can operate completely unattended for short periods, with probes determining the position of the plants, although it would normally be staffed by two people.
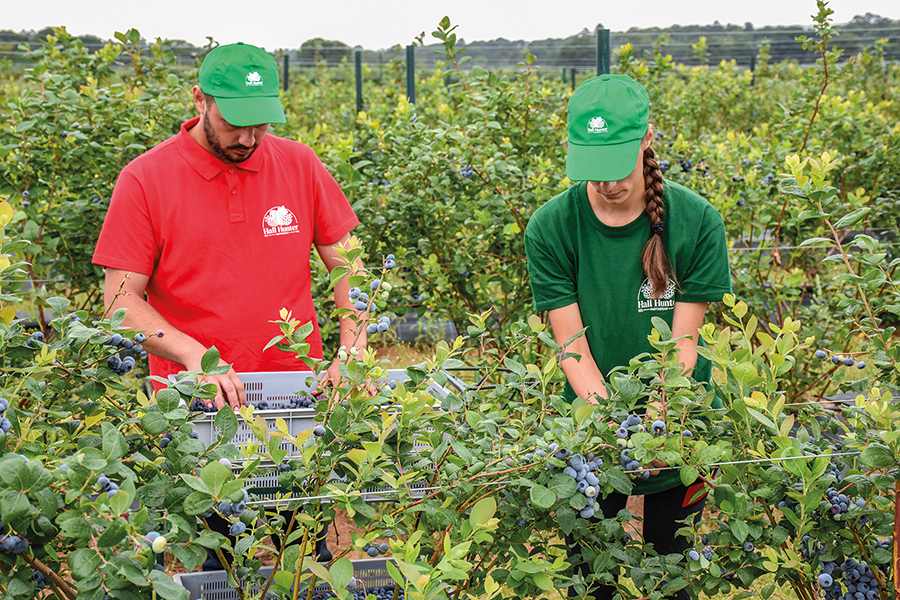
During these early days, while there is still a little fine tuning to be done, Hall Hunter is using a team of four, with two following up behind hand-picking any berries that were missed.
There was also a certain number of berries lost to the ground and a number of unripe berries, together with a little bit of foliage, ending up in the trays, despite the air stream system that is designed to remove leaves and twigs just before they enter the trays. These are all things that will gradually be improved upon with slight modifications to the machine, and the development of the crops specifically designed for machine harvesting. Even so it was an impressive sight watching the machine at work and seeing how quickly the trays were filling.
There is a computer on board that ensures that the four wheels are continuously at the right height, and it is self-levelling, so the machine remains perfectly vertical, regardless of the surface. At the same time, the load-bearing capacity per wheel is measured and regulated, so there are no unwanted forces on the frame and the traction is always perfect.
An onboard internet connection allows the machine’s current status – such as harvesting data, e.g. kg per hour, kg per bush and kg per row, as well as the position of the machine in the field – to be monitored from, and reported to, the machine’s HQ.
After completing the harvesting of one row, a set of four wheels drop down to allow the machine to move sideways to the next row before being retracted and off it goes again.
The whole thing is controlled remotely from a wireless control box by one of the operators and is powered by Li-Ion batteries that run two energy-efficient electric motors. The batteries are charged from a large array of solar panels on the top, providing quiet, emission-free running.
On cloudy days, a small internal combustion engine generator provides additional power to keep the machine running, should the batteries run low. Of course, unlike manual pickers, the machine could operate 24/7, if required and can work at speeds ranging from 100 metres per hour up to 700 metres per hour.
Despite the initial investment cost, and the fact that even with the refinements Jim is hoping to see there will still be a greater loss of berries on the ground and a higher number of unripe berries picked than with hand picking, the savings in labour costs will be so huge that Jim would like to see four or five of the machines roaming the farm.
Autonomous robot
On the day of F&V’s visit, a new kind of automation was being trialled and demonstrated. The Fox Robotics Hugo RT is an autonomous mobile robot designed specifically for the purpose of transporting soft fruit.
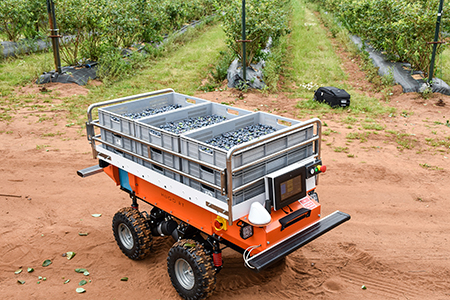
The Hugo RT can be programmed to independently travel between the field and the fruit storage, sorting or packing area using pre-programmed mapping data. It can carry up to 200kg of fruit and tow a trailer behind of up to 500kg. It uses GPS for location planning, and cameras and collision sensors to avoid obstacles.
Its location can be monitored using an app so, with perhaps a fleet of them running backwards and forwards, the Harvy 500 operators can see where they are and be ready for offloading empty crates and reloading full ones, keeping the Harvy running almost continuously. The Hugo is powered by two rechargeable batteries and has a top speed of up to 10kph. The RT in its name stands for rough terrain, so it should have no trouble dealing with the typical lumps and bumps found on farm tracks and between the rows of fruit.
Grading and packing
Once the berries are delivered from the field to the packing area, another new autonomous machine is used to grade them and remove those that are unripe or damaged.
The Elifab is a blueberry grading and packing machine that utilises AI technology to sort through the crop at a high rate. The first stage removes the green unripe berries and any that are obviously damaged. Then a second stage removes any ‘B’ grade fruit that does not meet the requirements for Hall Hunter’s premium customers.
The best berries are then passed into hoppers where the exact required weight is measured before they drop into punnets below. These are then passed through a process that places a cellophane lid on the punnet before they go through a final check to ensure the weight is correct.
Any found to be underweight are quickly rejected before the punnets that pass get delivered to a final packing station to be stacked and crated up ready for collection and delivery to the supermarkets. It is really only this final stage, and the loading of the full crates at the beginning, that requires any human input beyond a skeleton staff for monitoring processes as the berries go through the process.
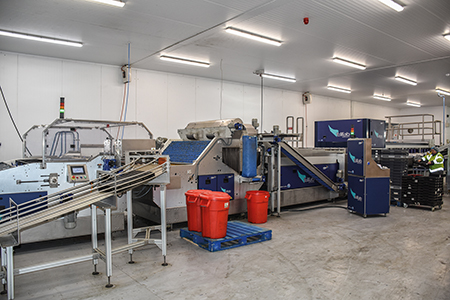
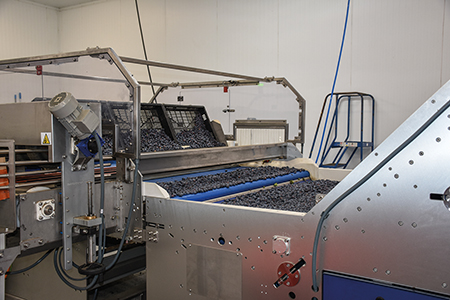
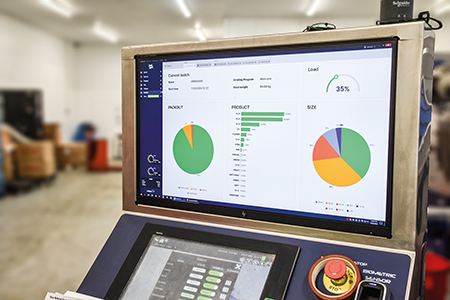
Huge technology investment
As already mentioned, Hall Hunter is a visionary grower – but it’s not just through the use of autonomous machines. Elsewhere on the farms, huge investment has been made in a heating system for the polytunnels.
When Hall Hunter took over Tuesley Farm they installed a system that takes residual heat from an on-site 150 million litre reservoir using heat exchangers, as found in ground source or air source heating systems.
The heat is used to warm water that is then pumped via pipework into the polytunnels, where they grow 26ha of strawberries in heated conditions. Despite the fact that in the depths of winter the surface of the reservoir can be frozen over, they can still extract 4-5°C out of the water deep at the bottom using equipment housed in specially-built machine rooms.
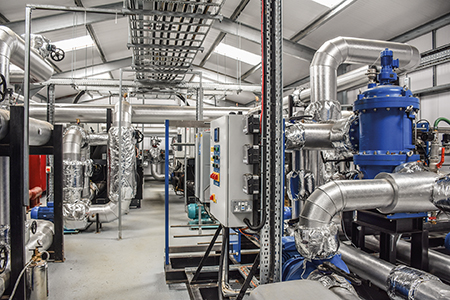
The 4–5°C taken from the water is increased via the pump system to 45°C, creating a significant rise in temperature beyond the 5°C taken.
Each one of these machine rooms represent a multi-million pound investment, and they have one at each of their three farms; but the payback is that they give a reduction in heating costs and allow the farms to produce early and late fruit for premium markets. In the summer, the reservoirs, which are naturally fed and filled, are used for irrigation.
With demands for less chemicals and more organic methods in farming generally, Hall Hunter has planted the unfarmed areas of the farm, around the perimeters of the poly tunnels for example, with plants and flowers specifically chosen to attract wildlife that help naturally keep pests under control.
Hall Hunter also houses five million bees, both honey and bumble, to help with pollination, particularly of the blueberries. A beneficial bi-product of this, in addition to the increased pollination and crop sizes, is that the company can offer its own-branded honey.
The company is proud not only of its traditions and heritage, but of also consistently working to implement new technologies to execute the best and most efficient harvests possible.
Read more machinery news