Improved grape quality justifies harvester investment
16th November 2022
A long-established Essex vineyard which produces high quality wines made from grapes grown on site has invested in a brand new self-propelled grape harvester.
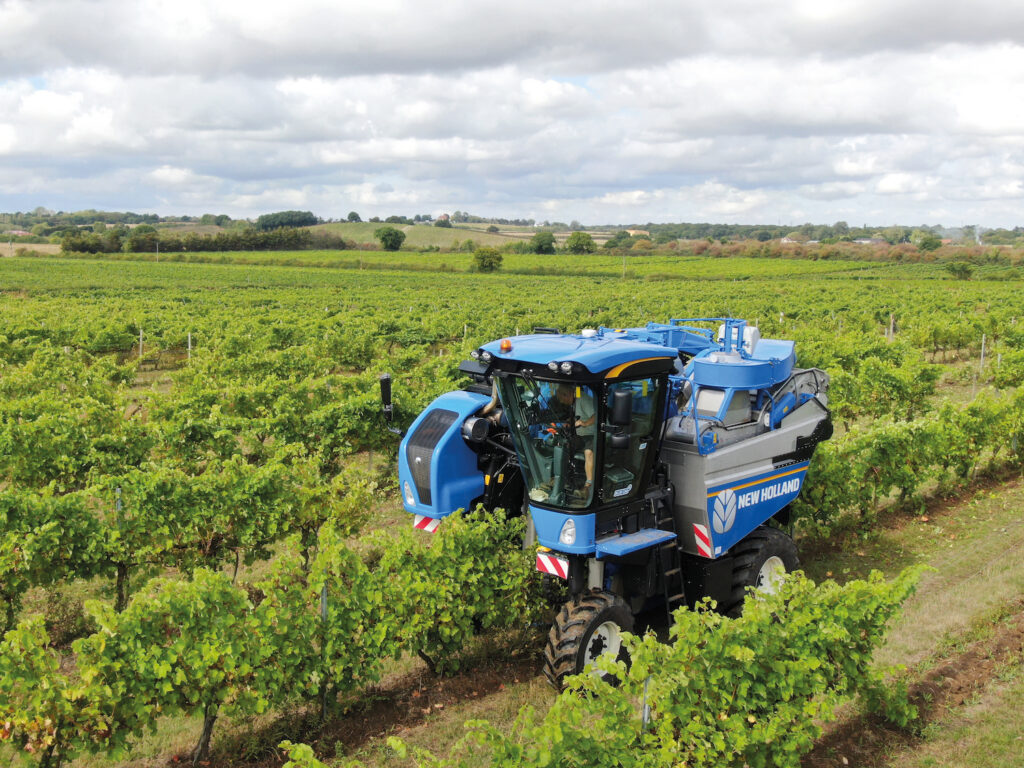
An Essex-based producer of fine quality wines has invested in a New Holland Braud 9090X grape harvester to ensure the crop can be picked in optimum condition and delivered promptly to the onsite winery.
Owned by the Greenwood Partnership, New Hall Wine Estate in Purleigh in the Crouch Valley is one of England’s oldest commercial vineyards. Wine-making started there in 1969, and it remains in the same family’s ownership, managed by the third generation. There are currently 31 plantations and 50ha of land under vines, and further expansion is planned. The vineyard produces 16 varieties of grape, including Bacchus grown on some of the first Bacchus vines established in the UK more than 40 years ago.
Until a few years ago, some fruit was sold for wine production elsewhere, but increased demand for New Hall wines and recent investment in a state-of-the-art onsite winery has led to increased production and sales. Now all the fruit is pressed, crushed, fermented and bottled at New Hall, and the range of wines includes winners of significant awards.
Quality the priority
“Our primary objective is always to grow the very best fruit and harvest it in optimum condition for our winemakers to produce excellent wines,” explained vineyard manager Andy Hares. “For a single site UK wine producer our enterprise is quite large, and we don’t have the advantages of many more modern vineyards where all the vines are laid out and spaced perfectly on commercially produced trellises, and with lots of space between rows and at the ends for modern machines to turn around. Many of our vineyards were laid out when all the work was done by hand, so we continue to rely on traditional practices and manual labour.”
Employing teams of up to 40 pickers for the short harvest period meant that grapes were picked continuously, to keep the team of seasonal workers busy and ensure that all the plantations were picked in the time available. Disadvantages included an uneven supply of fruit to the winery, and that some grapes were harvested before reaching optimum condition.
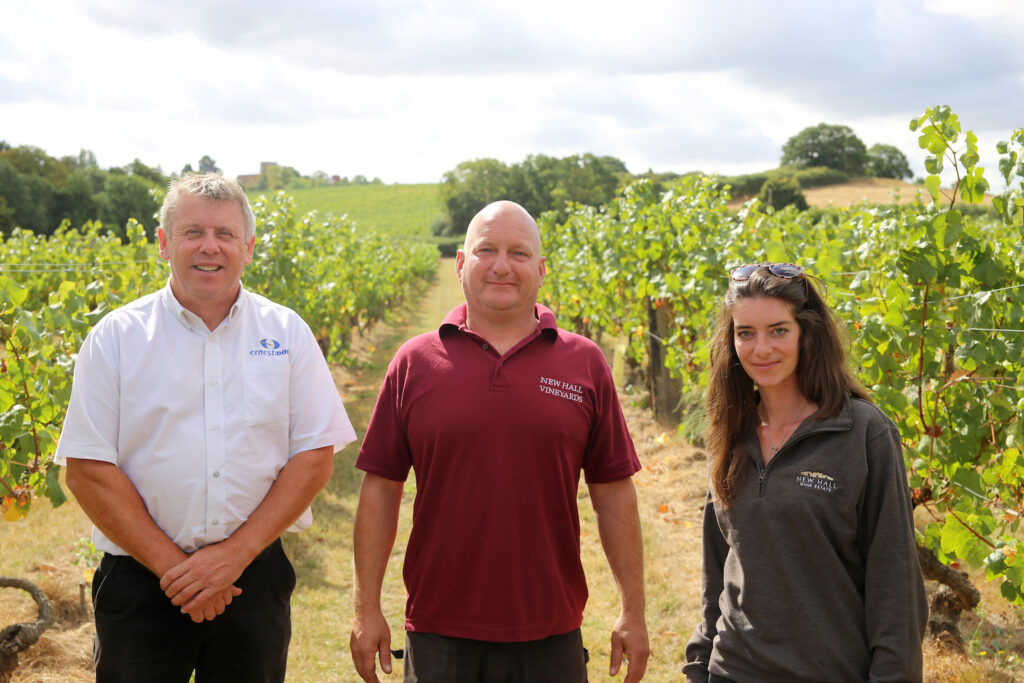
Pictured (l-r) Ernest Doe area sales representative, Derek Peck; New Hall Wine Estate vineyard manager Andy Hares; and New Hall Wine Estate general manager, Becki Trembath.
Preserve quality
“We believed that investing in a self-propelled harvester would give us extra flexibility,” said Andy. “Higher work rates would allow us to fill the grape bins quickly and deliver them to the winery for processing in the shortest possible time – reducing any loss of quality through oxidation. Knowing we have the capacity to harvest them at the optimum time would also mean we could leave grapes hanging on the vines for longer while the sugars develop, and that would result in more versatile fruit and allow our winemakers to do more with them.”
Wide experience
Andy has managed the New Hall vineyards for seven years, and before that he worked for 10 years on vineyards in France. “Mechanical harvesters are widely used in mainland Europe, and I had seen the gains in harvested grape quality and improved working efficiency they provide. Although many of our plantations are not ideal for machine working, our more recently planted areas are suitable, and then we also have plantations which could be adapted in time.”
Confidence in back-up
The New Holland Braud grape harvester was the preferred brand for its reputation in Europe, as well as its gentle crop handling and build quality. “We already had an excellent relationship with the Ernest Doe Ulting depot team, and operate New Holland tractors,” explained Andy. “A new grape harvester represents a significant investment, so we had to be sure that back-up will be available if problems occur.
“We were very pleased by the reaction of the dealer as well as the team at New Holland UK, so we ordered New Holland’s 9090X flagship model which arrived in early September.”
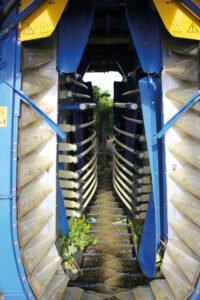
The 24 horizontal bars shake the vines. New Holland’s Shaking Dynamic Control allows the intensity to be adjusted for the variety and conditions. The exclusive Noria collection system consists of a chain of polyurethane buckets which effectively clamp the vine stems and create a seal so that grapes and juice end up in the buckets rather than on the ground.
Premium specification
The New Holland Braud 9090X removes grapes from the vines using 24 horizontal flexible bars – 12 on each side – which shake the vines vigorously at a frequency of 470–480 movements per minute, and without causing damage. New Holland’s Shaking Dynamic Control allows the operator to finely tune the shaking action to suit the crop and conditions. Falling grapes are caught by the Noria bucket system – a chain of close linked polyurethane buckets below the shaker bars on each side, which move at ground speed. The flexible buckets seal around each plant stem close to ground level along the full 2.5m length of the shaker bars. They catch the grapes and juice and carry them up to the cleaning system.
The harvesting module or header containing the shaker bars and buckets moves independently of the main chassis, and automatically maintains a vertical working position to follow the vine angle rather than the ground, on side-slopes up to 30%.
Grape stems are removed by a mesh conveyor and spider wheels, without damaging the grapes. The stems are discharged at the rear, then the grapes travel through airflow from four adjustable fans which gently clean the crop and remove remaining loose stems and leaves.
Clean grapes are delivered into stainless steel hoppers on each side with a combined 4,000-litre capacity, and leaves and other light materials are blown through two exhaust chutes and discharged at the rear.
The two grape hoppers are hinged at the rear, and tip for unloading. Tipping is activated from inside the cab, or from outside by a Bluetooth-linked remote control.
Save working profiles
The main functions are controlled by an armrest-mounted joystick, and the New Holland IntelliView 4 touchscreen terminal provides performance information and is used to set up and adjust the machine. Settings can be saved as profiles for different plantations and varieties, and conveniently selected again in future years. A network of cameras allows the operator to monitor the crop’s progress through the machine as well as the quality of grapes in the hoppers.
The harvester is powered by an FPT engine developing 182hp, and hydrostatic transmission allows infinitely variable speed control. Drive is automatically distributed to the wheels with most traction to reduce wheel slip, and to compensate for sideslip on cross slopes. For transport only the front wheels drive and maximum speed is 30kph.
Technique involved
Andy quickly got used to the machine. “The first opportunity I had to try it was when the grapes were ready for harvesting and, although I knew the basics, I struggled to achieve good results. New Holland’s grape harvester specialist, Philippe Boisseau, travelled to England and helped me set up the machine. There is a lot of technique involved, and as soon as he demonstrated the correct procedure for setting up the machine, operating it became much easier. Very small changes to the settings make a big difference.”
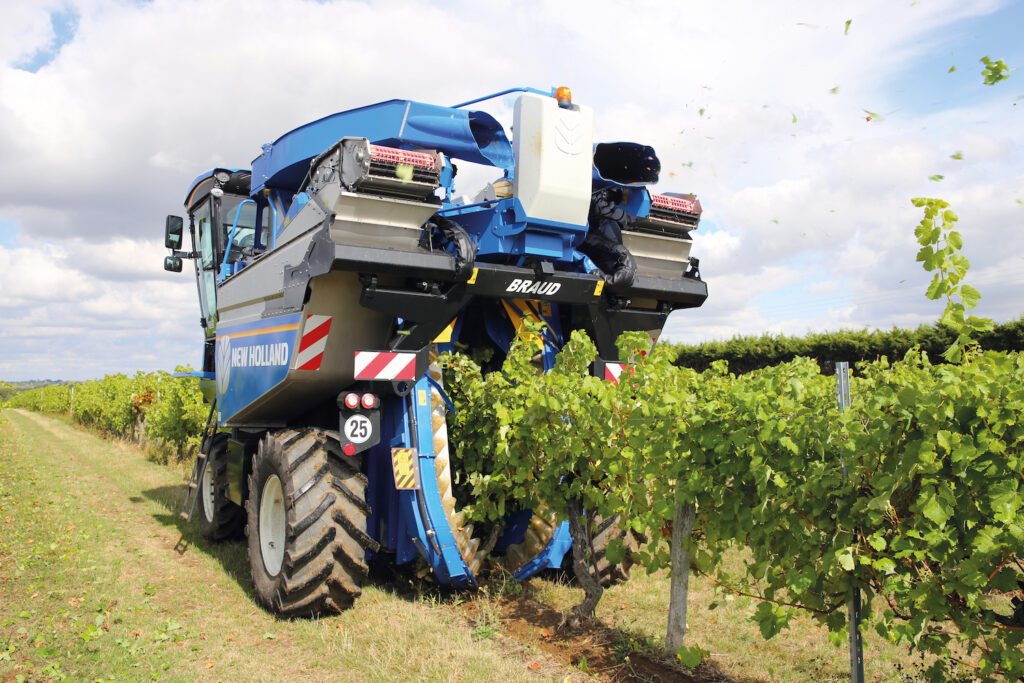
Powerful fans create airflow to remove lighter materials such as leaves and loose stems which are then discharged through a pair of outlets at the rear
High work rates and high quality
“We were all amazed by the quality of the harvested fruit, and particularly the clean sample and lack of damage. Experienced pickers each achieve 400–450kg per day, but the New Holland picks more than 7,000kg in 3.5 hours, and achieves this operating at a modest 2.0–2.5kph although the recommended speed is 3.0–4.5kph, and it will work at 7.0kph when conditions are ideal.
In theory, it could complete our whole harvest in only 70 working hours, and knowing we had that sort of capacity available contributed to a more relaxing season. We were able to deliver just as much fruit as was required by the winery team, then wash the machine down and do something else until more grapes were needed. In hot weather we harvested early in the mornings and in the late afternoons – avoiding the mid-day period when temperatures were higher and the quality of harvested fruit declines most quickly.”
Very efficient
Wastage has also been reduced, continued Andy. “Varieties such as Bacchus are difficult to pick by hand as the bunches are well hidden by leaves, so we usually find a lot left on the vines which were missed during manual harvesting. The New Holland gets almost all of them, and there are very few lost through the cleaning system either. It’s very efficient.”
Asked whether the older plantations have caused problems for the machine, Andy said there have been fewer than expected. “Where we have sleepers or concrete posts which are wider than the gap between the shaker arms and the two rows of buckets there was no point trying as the machine would have been damaged, but even where the narrow concrete end posts were at an angle, the machine coped well. We have been able to use it in some areas where we thought we would have to pick by hand, and the experience gained this season means we know what additional pruning and trellis modifications are needed for next year.
“The vines themselves have suffered very little damage during harvesting. Obviously, they were planted and pruned with manual picking in mind in the past, but the flexible shaker rods followed the rows well. The New Holland Braud design is very effective.”
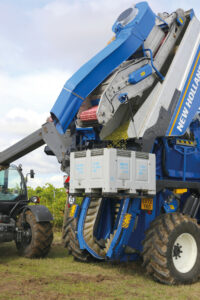
A pair of stainless-steel hoppers hold up to 4,000 litres of grapes, but the machine’s high work rate meant there was little time pressure, and the hoppers were emptied frequently to reduce damage and minimise the time between picking and delivery to the winery.
Quick acceptance
Andy said that although some members of the vineyard team were concerned when mechanical harvesting was first suggested, it didn’t take long for everyone to become convinced of the benefits once the machine started work.
“Most importantly, our winemakers are very impressed by the sample we are delivering into the winery,” he stressed. “The harvester simply improves the quality of what we already have here, and it allows us to pick at the point which is best for the fruit – not just when we have labour available. We made the investment to maximise our grape and wine quality, but an additional benefit is that we can operate with a smaller team of just 10–12 manual pickers, so management
has been easier, too.”
Increasing demand
“Demand for small tractors and specialised machines for vineyard use has increased considerably in recent years,” explained Ernest Doe area sales manager, Derek Peck. “We are very pleased to have supplied New Hall Wine Estate with the first New Holland Braud grape harvester sold new in the UK and believe it will provide major benefits for this long-established business.
“We are working closely with New Holland to ensure that we can provide back-up for the grape harvester whenever it is needed and have already invested in product training for several of our engineers so that they understand its design and operation.”